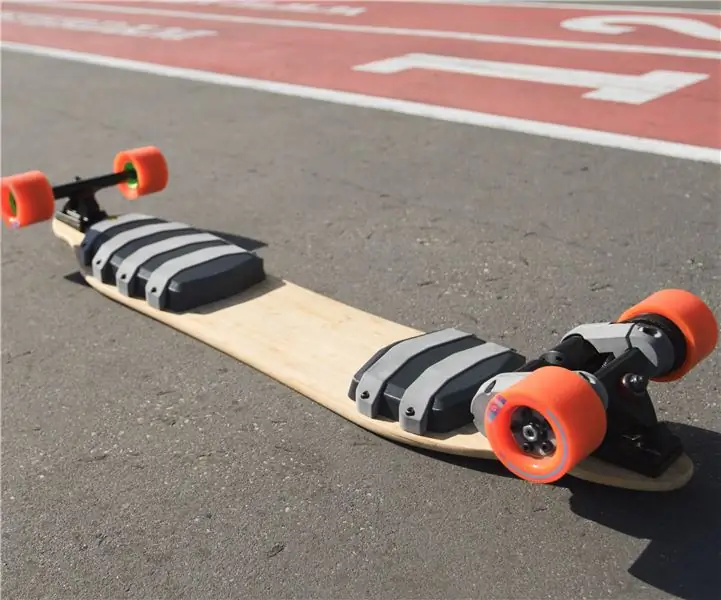
Съдържание:
2025 Автор: John Day | [email protected]. Последно модифициран: 2025-01-23 14:36
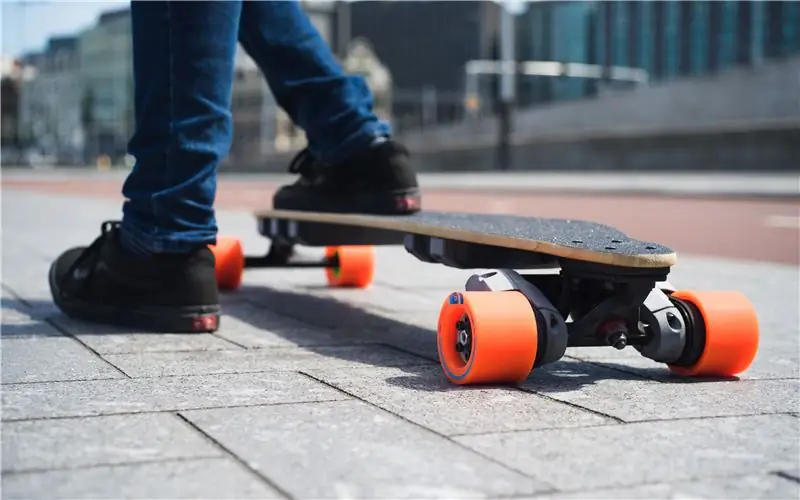
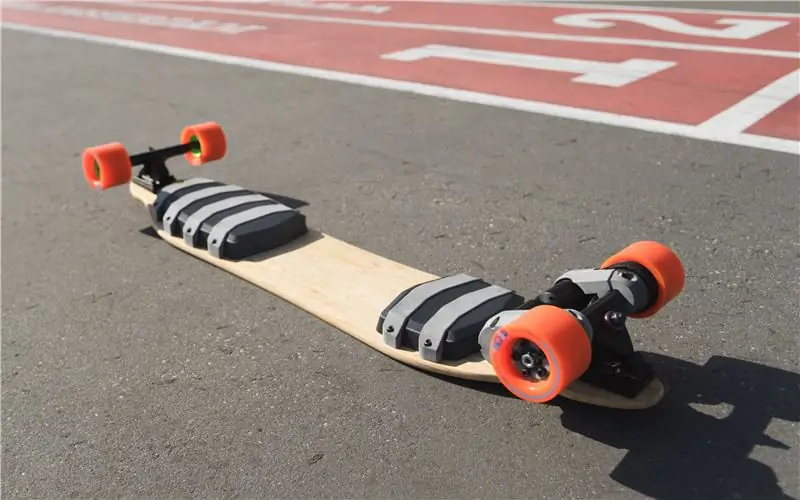
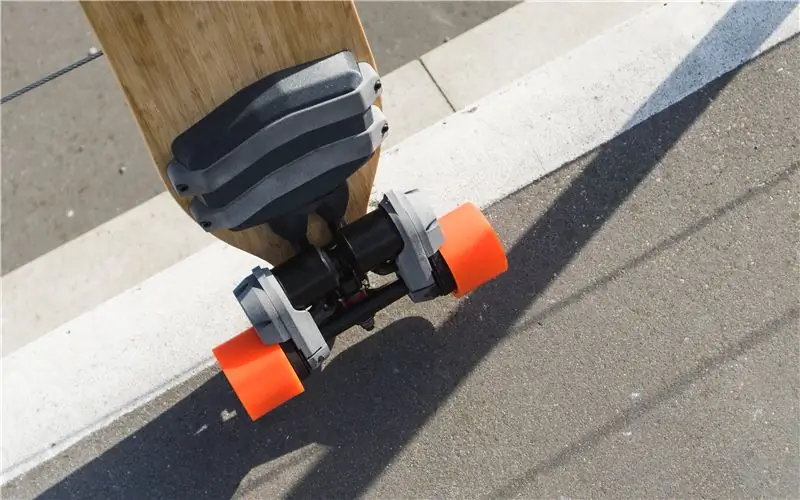
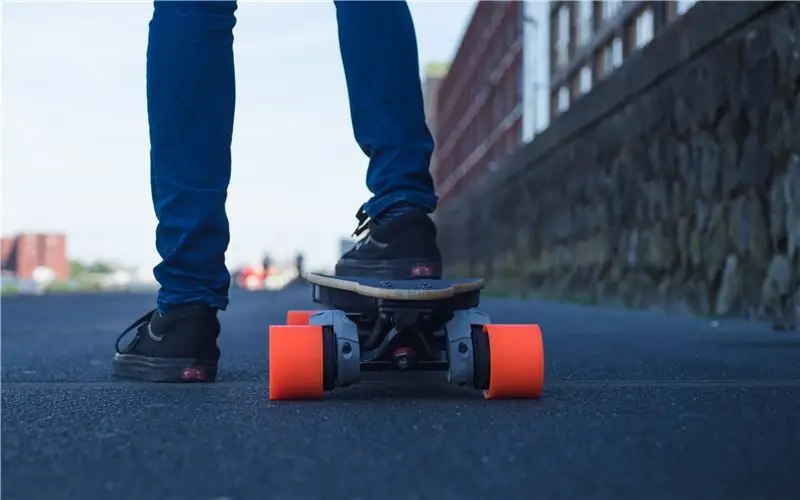
Този Instructable е преглед на процеса на изграждане на Fusion E-Board, който проектирах и изградих, докато работя в 3D Hubs. Проектът е възложен за популяризиране на новата технология HP Multi-Jet Fusion, предлагана от 3D Hubs, и за показване на множество технологии за 3D печат и как те могат да бъдат ефективно комбинирани.
Проектирах и изградих електрически моторизиран лонгборд, който може да се използва за кратки до умерени пътувания или да се комбинира с обществен транспорт, за да предложи много по -широк обхват на пътуване. Той има висока максимална скорост, много е маневрена и лесно се носи, когато не се използва.
Стъпка 1: Процес на проектиране
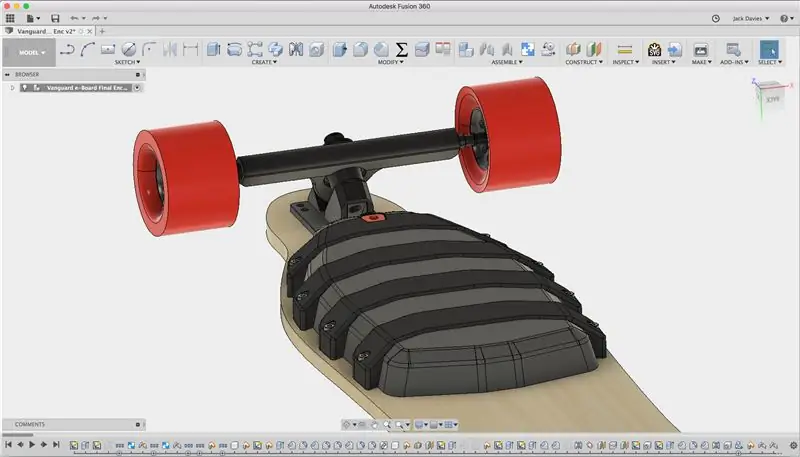
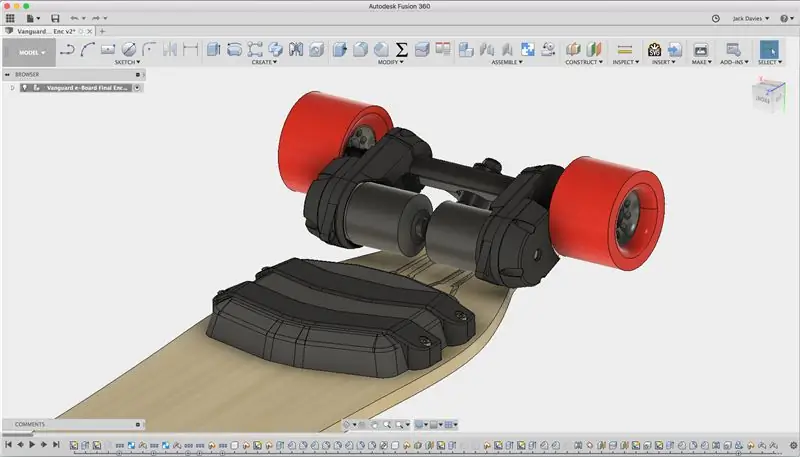
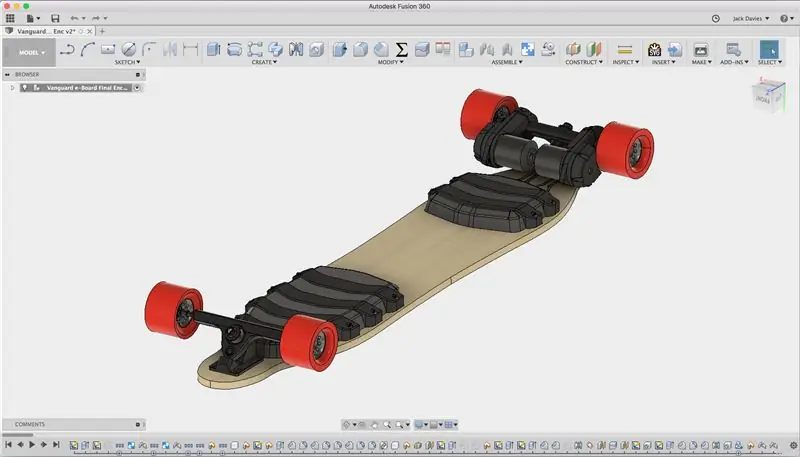
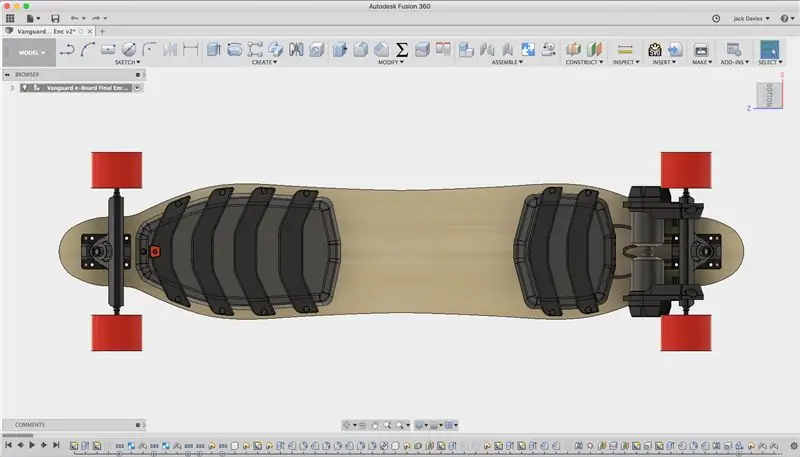
Започнах проекта, като идентифицирах основните стандартни компоненти на лонгборда; камиони, палуба и колела. Това бяха части от рафта, затова ги използвах като отправна точка на дизайна. Първият етап беше проектирането на задвижващия механизъм, това включва опорите на двигателя, настройката на предавките и включва някои модификации на камионите. Размерът и позицията на опорите на двигателя ще диктуват размера и местоположението на загражденията, така че беше важно това да бъде завършено първо. Изчислих желаните изисквания за максимална скорост и въртящ момент, което след това ми позволи да избера двигателите и батерията за платката. Съотношението на предавките също беше изчислено и бяха избрани размерите на ролките, заедно с дължината на задвижващия ремък. Това ми позволи да изработя правилния размер на стойките на двигателя, което осигури добре опънат колан.
Следващият етап беше проектирането на корпусите на батерията и регулатора на скоростта (ESC). Избраната палуба се състои предимно от бамбук, така че е доста гъвкава, огъваща се значително по средата. Това има предимства, че е удобно за каране, тъй като абсорбира неравностите по пътя и не ги прехвърля на ездача. Това обаче също така означава, че е необходимо разделяне на корпуса, за да се поместят батерията и електрониката, тъй като корпусът в цяла дължина няма да може да се огъне с дъската и ще влезе в контакт със земята по време на работа. Електронните регулатори на скоростта (ESC) бяха поставени най -близо до двигателите поради електрически ограничения. Тъй като двигателите са прикрепени чрез камионите, позицията се променя по време на завои, така че заграждението трябва да бъде проектирано така, че да позволява освобождаване на двигателите.
Батерийната система беше поставена в другия край на палубата и побираше електрониката, свързана с захранването. Това включва батерията, състояща се от 20 литиево -йонни клетки 18650, системата за управление на батерията, превключвателя за включване/изключване и гнездото за зареждане.
Използвах Autodesk Fusion360 за целия процес на проектиране, този софтуер ми позволи бързо да моделирам компоненти вътре в основния монтаж, което значително ускори времето за разработка. Използвах и симулационните функции във Fusion360, за да гарантирам, че частите ще бъдат достатъчно здрави, особено опорите на двигателя. Това ми позволи действително да намаля размера на стойките, тъй като можех да проверя изискванията за якост и отклонение и да премахна материала, като същевременно поддържам подходящ коефициент на безопасност. След приключване на процеса на проектиране беше много лесно да се експортират отделните части за 3D печат.
Стъпка 2: Задвижване
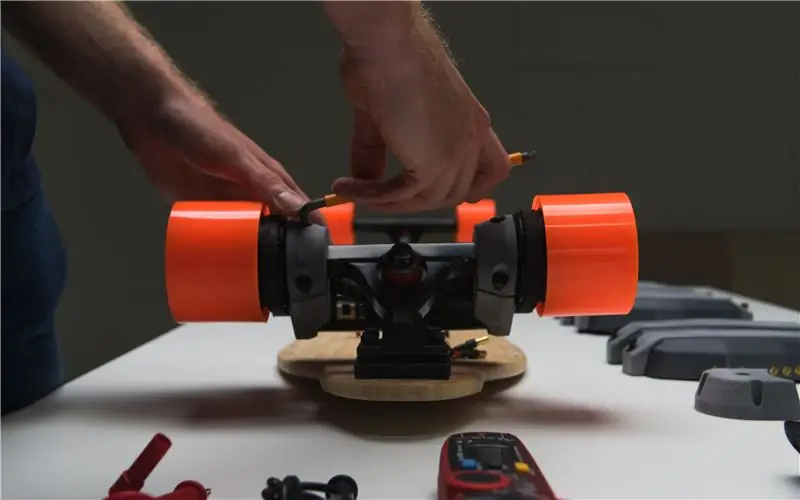
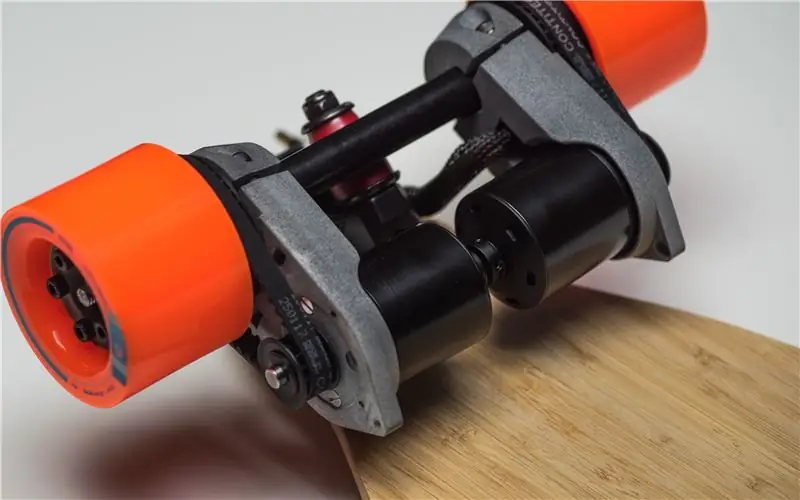
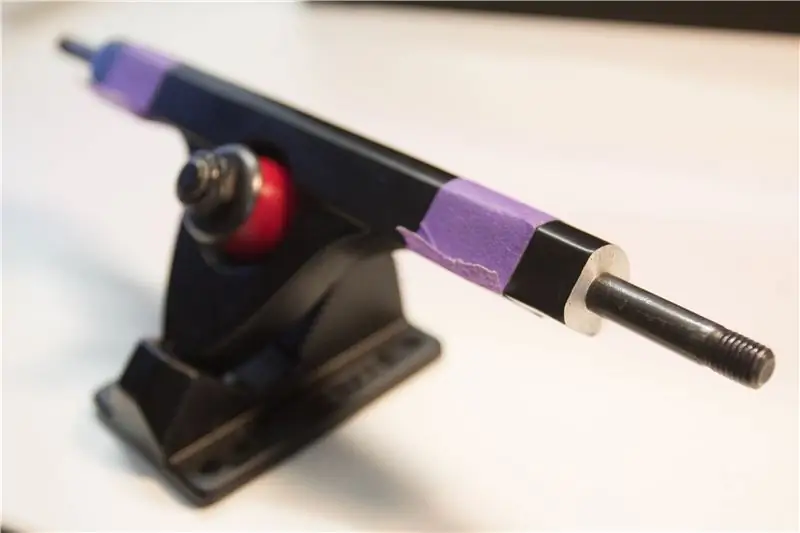
Първо завърших изграждането на задвижването, за да осигуря подходящ хлабина за корпуса на електрониката. Избрах камиони Calibre за използване, тъй като те имат квадратен профил, който беше идеален за закрепване на опорите на двигателя. Оста обаче беше малко прекалено къса, за да позволи на двата двигателя да се използват на един и същ камион, така че трябваше да удължа това, за да позволя на колелата да се поберат.
Постигнах това, като отрязах част от алуминиевата закачалка на камиона, излагайки повече от стоманената ос. След това отрязах по -голямата част от оста, оставяйки около 10 мм, които след това мога да резба с матрица M8.
След това може да се завинтва съединител и към него да се добави друга резбова ос, което ефективно удължава оста. Използвах Loctite 648 задържаща смес, за да закрепя трайно съединителя и новата ос, за да се уверя, че няма да се развие по време на употреба. Това позволи на двата двигателя да се поберат на камиона и осигури достатъчно свободно пространство за колелата.
Задвижващият механизъм е отпечатан предимно с помощта на технологията HP Multi-Jet Fusion, за да се осигури твърдост и здравина по време на голямо ускорение и спиране, където ще бъдат прехвърлени най-големите сили.
За закрепване на задните колела е проектирана специална ролка, която след това е свързана към ролката на двигателя с колан HTD 5M. Добавен е 3D отпечатан капак, за да се осигури защита на шайбата.
Стъпка 3: Корпуси на ребрата
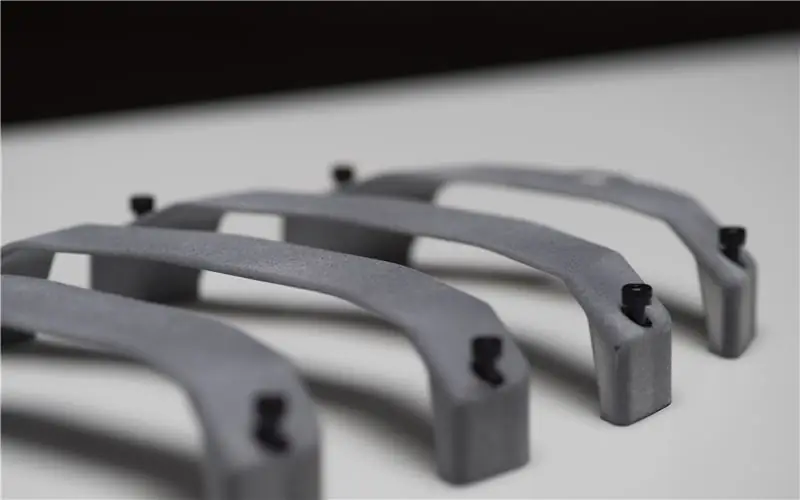
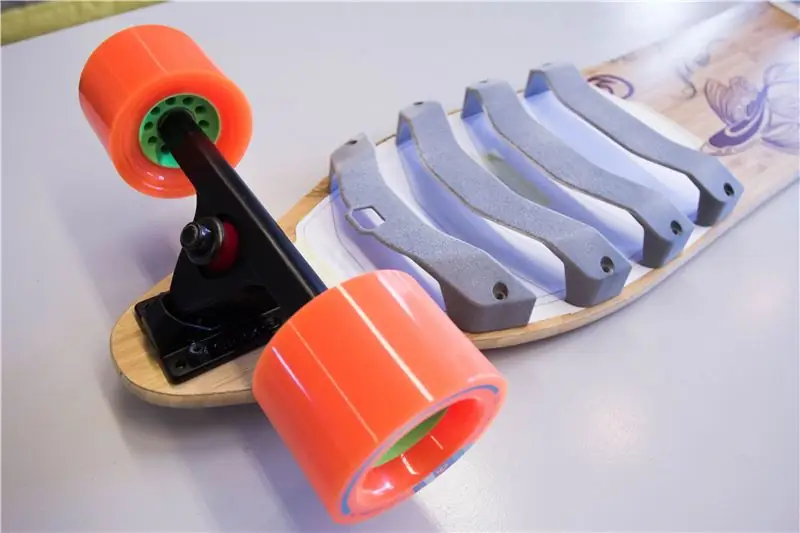
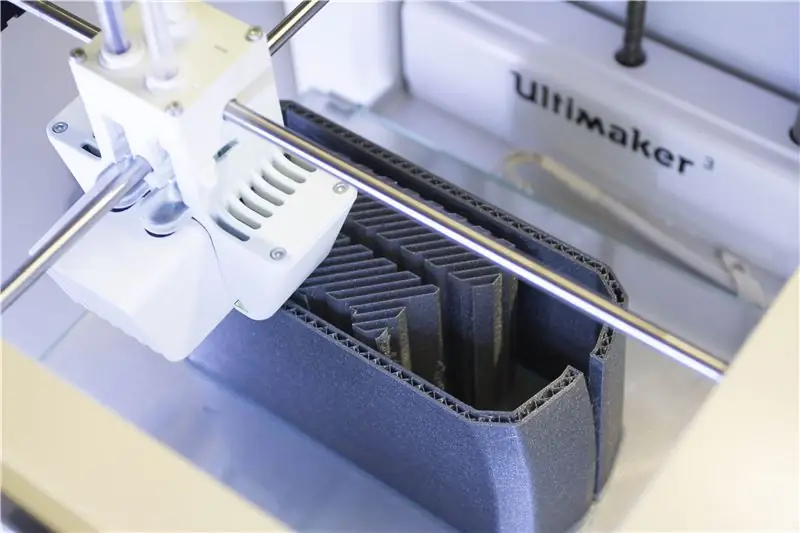
Едно от основните дизайнерски решения, които взех, беше да отделя загражденията, което доведе до чист вид и позволи на гъвкавата палуба да функционира без никаква допълнителна твърдост от загражденията. Исках да предам функционалните аспекти на технологията HP Multi Jet Fusion, затова реших да отпечатам FDM основното тяло на корпусите, което намали разходите, а след това използвах частите на HP, за да ги поддържам и закрепвам към палубата. Това осигури интересна естетика, като същевременно беше и много функционална.
Отпечатаните кутии с FDM бяха разделени наполовина, за да помогнат при печат, тъй като поддържащият материал може да бъде елиминиран от външната повърхност. Разделителната линия беше внимателно позиционирана, за да се гарантира, че е скрита от частта HP, когато е прикрепена към дъската. Бяха добавени дупки за съединенията на двигателя и бяха залепени на място позлатени конектори за куршуми
Вложките с резба бяха вградени в бамбуковата палуба, за да закрепят корпусите към дъската, и бяха шлифовани на едно ниво с повърхността на дъската, за да се гарантира, че няма празнина между палубата и корпуса.
Стъпка 4: Електроника
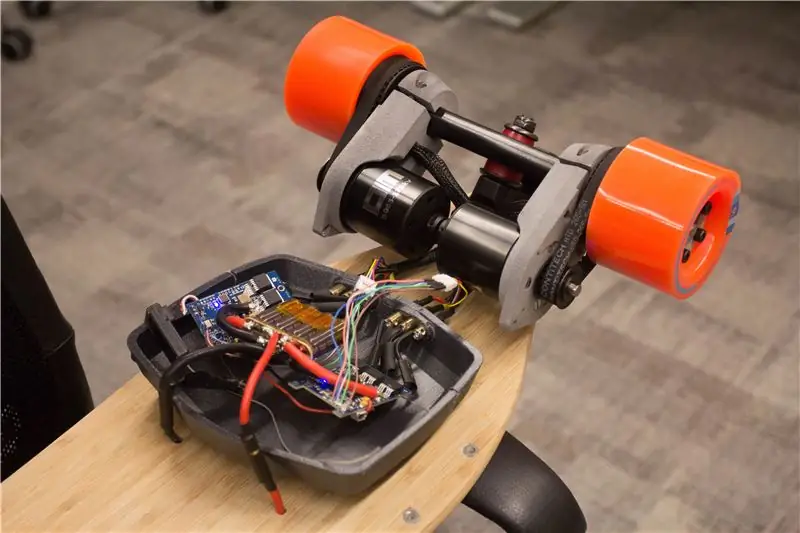
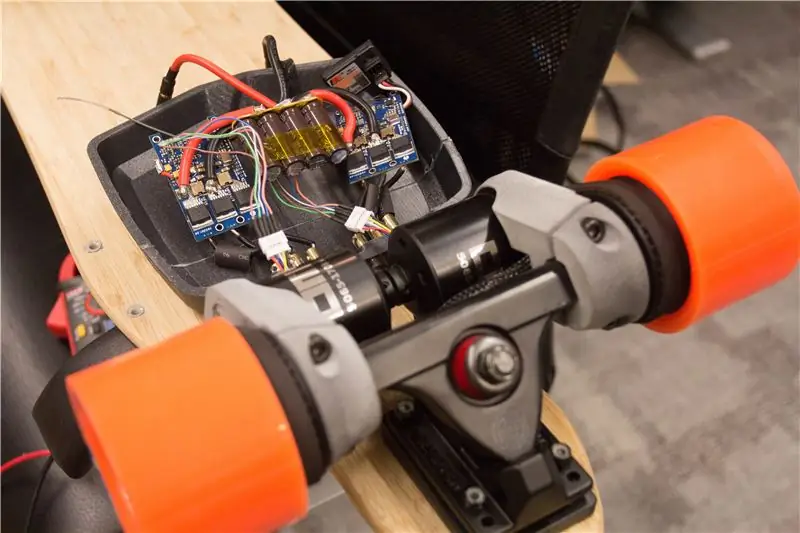
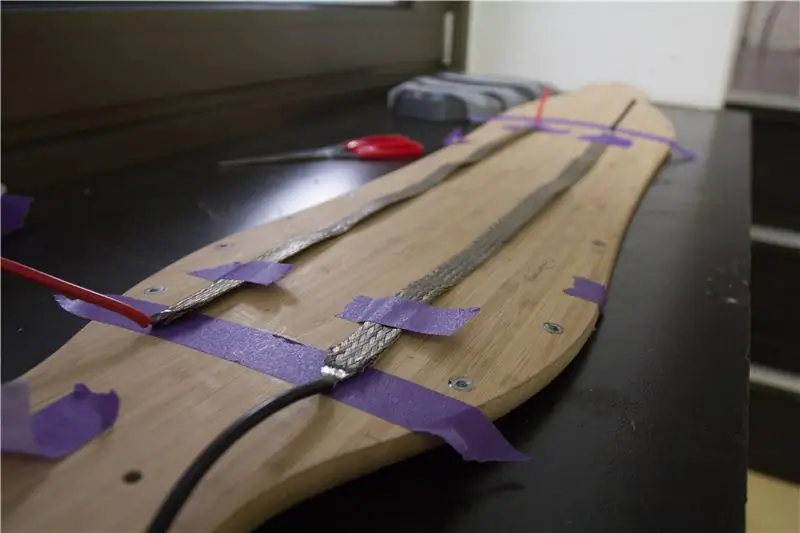
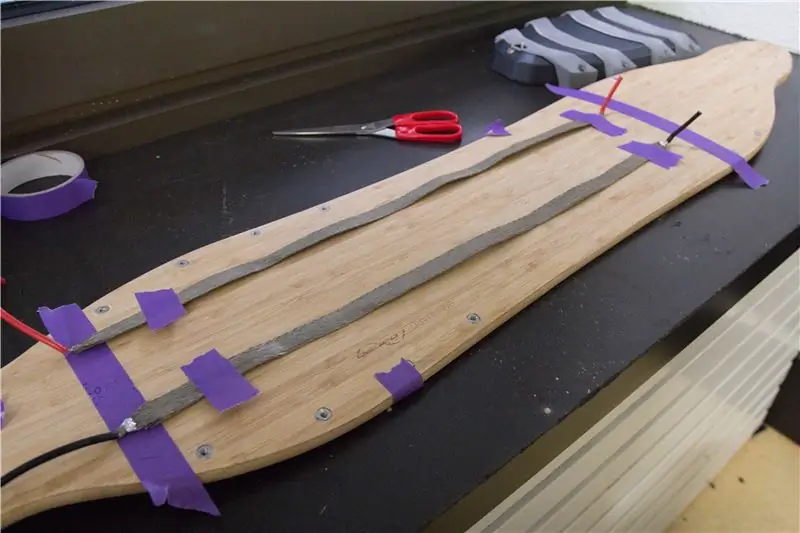
Електрониката е внимателно подбрана, за да се гарантира, че дъската е мощна, но и интуитивна за използване. Тази платка може потенциално да бъде опасна, ако възникнат някакви неизправности, така че надеждността е много важен фактор.
Батерията се състои от 20 отделни 18650 литиево-йонни клетки, които са споени заедно, за да образуват 42v пакет. 2 клетки са заварени паралелно и 10 последователно; клетките, които използвах, бяха Sony VTC6. Използвах точков заварчик, за да заваря никеловите пластини, за да образувам опаковката, тъй като запояването създава твърде много топлина, която може да повреди клетката.
Захранването от кутията на батерията се прехвърля в кутията за регулиране на скоростта с помощта на плосък оплетен кабел, който се прокарва точно под захващащата лента от горната страна на палубата. Това позволи на кабелите да бъдат „скрити“и премахна необходимостта от прокарване на кабели от долната страна, което би изглеждало грозно.
Тъй като това е двойна платка на двигателя, са необходими два регулатора на скоростта за независимо управление на всеки двигател. Използвах регулатора на скоростта VESC за тази конструкция, който е контролер, специално проектиран за електрически скейтбордове, което го прави много надежден за тази употреба.
Използваните двигатели са 170kv 5065 out-runners, които могат да произвеждат 2200W всеки, което е много мощност за тази платка. С текущата настройка на предавките максималната скорост на дъските е около 35MPH и се ускорява много бързо.
Последният етап беше създаването на дистанционно за управление на дъската. Предпочита се безжична система поради по -лесната работа. Важно е обаче да се осигури висока надеждност на предаването, тъй като спадът в комуникацията може да има сериозни проблеми с безопасността, особено при високи скорости. След тестване на няколко протокола за радиопредаване реших, че 2.4GHz радиочестотата ще бъде най -надеждната за този проект. Използвах RC автомобилен предавател, но значително намалих размера, като прехвърлих електрониката в малък ръчен калъф, който беше 3D отпечатан.
Стъпка 5: Готово табло и промо видео
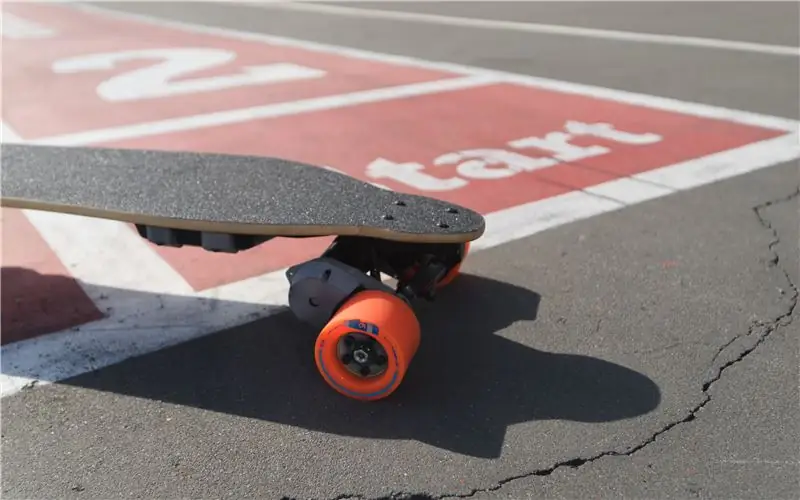
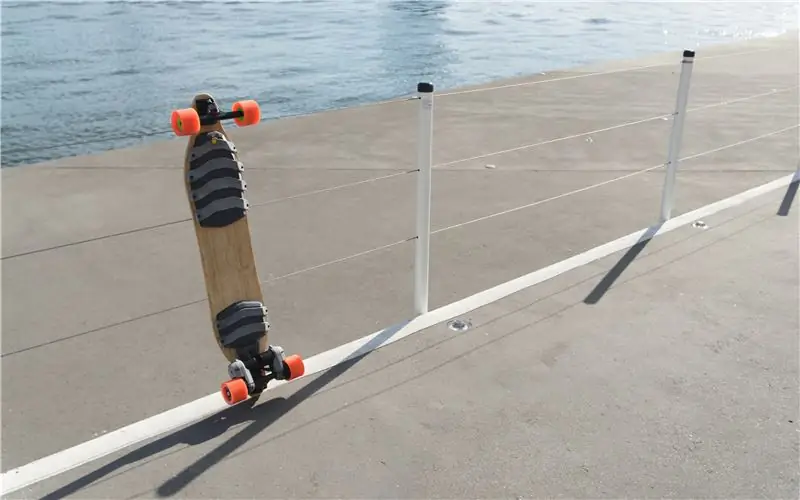
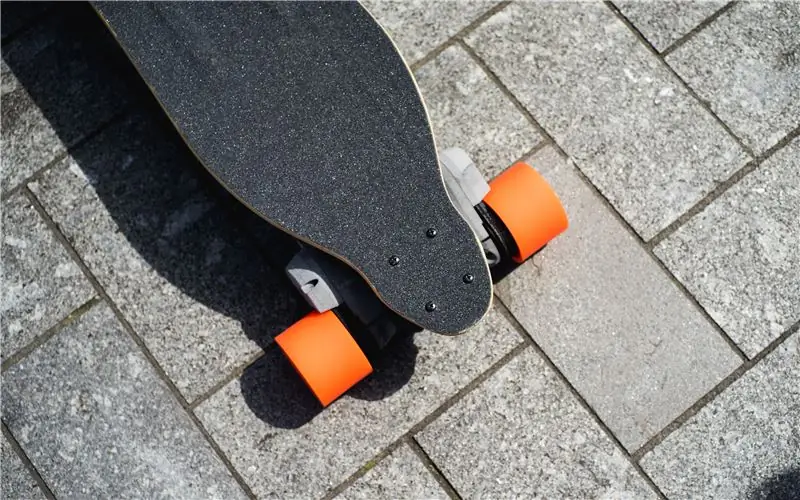
Проектът вече е завършен! Създадохме доста страхотно видео на борда в действие, можете да го проверите по -долу. Големи благодарности на 3D Hubs, които ми позволиха да направя този проект - проверете ги тук за всички ваши нужди от 3D печат! 3dhubs.com
Препоръчано:
Управлявайте мощен електрически скейтборд E-Bike 350W DC мотор, използвайки Arduino и BTS7960b: 9 стъпки
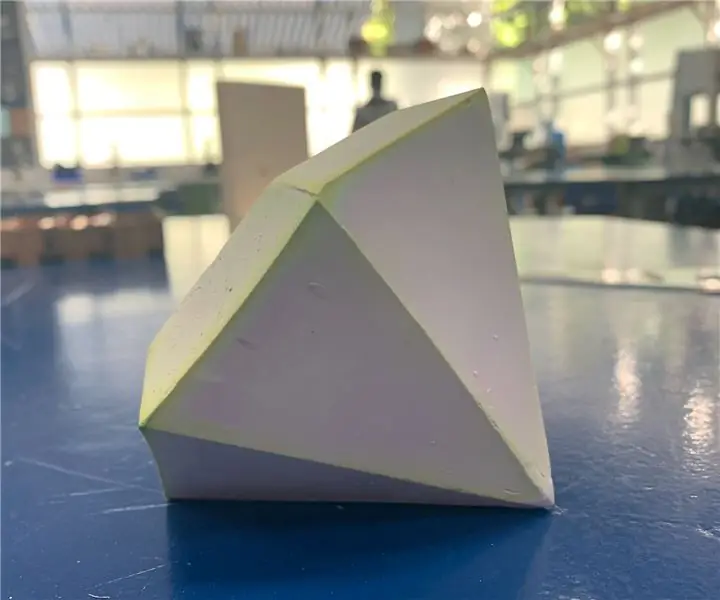
Управлявайте мощен електрически скейтборд E-Bike 350W DC мотор с помощта на Arduino и BTS7960b: В този урок ще научим как да управляваме DC мотор, използвайки Arduino и Dc драйвер bts7960b, Моторът може да бъде 350W или просто малък играчка arduino dc двигател стига мощността му да не надвишава максималния ток на драйвера на BTS7960b. Гледайте видеото
3D отпечатан електрически плъзгащ се превключвател (с помощта само на кламер): 7 стъпки (със снимки)
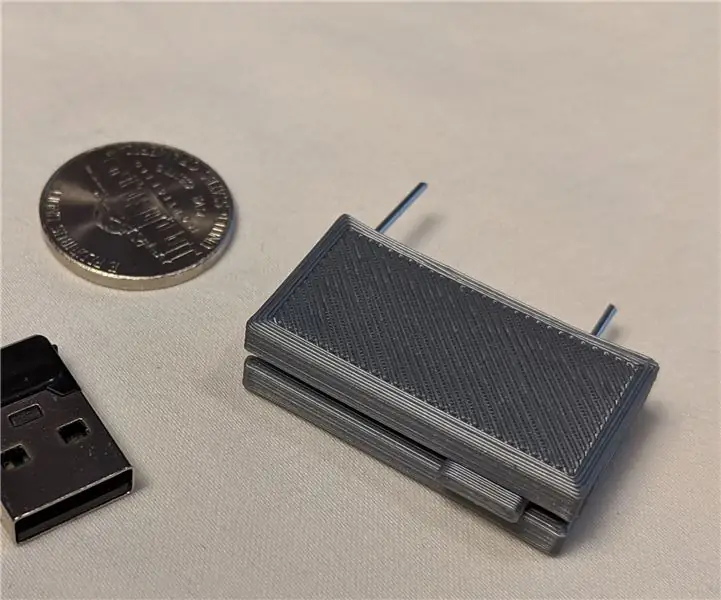
Електрически плъзгащ се превключвател с триизмерен печат (използвайки само кламер): През годините се опитвах да свържа моите собствени малки електрически проекти, най-вече под формата на кламери, алуминиево фолио и картон, покрити с горещо лепило. Наскоро си купих 3D принтер (Creality Ender 3) и тръгнах да търся
Спидборд: Електрически скейтборд: 5 стъпки
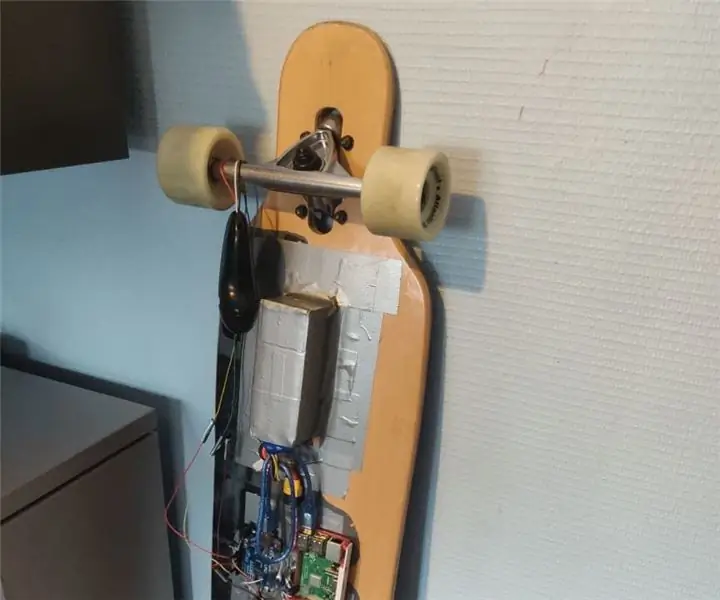
Спидборд: Електрически скейтборд: Здравейте! Аз съм студент от MCT College от Howest в Белгия. Днес ще ви дам стъпка по стъпка ръководство за това как да направите електрически скейтборд с малиново пи и arduino.Бях вдъхновен да направя този проект от известния youtuber на име Кейси Нейстат
Електрически одометър за скейтборд: 5 стъпки
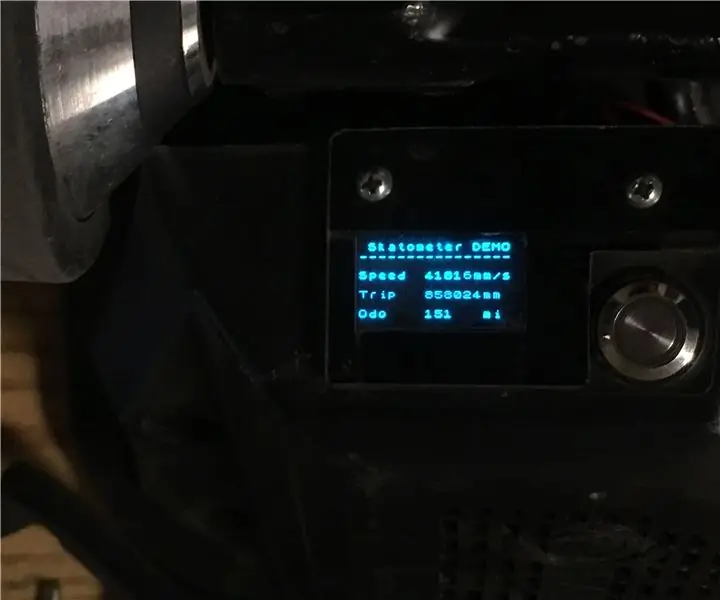
Електрически одометър за скейтборд: Въведение Повечето електрически скейтбордове от висок клас от около хиляда долара се предлагат с приложение за телефон, което показва информация за скейтборд в реално време и за съжаление по-рентабилните скейтбордове от Китай не идват с тях. Така че защо не
Електрически скейтборд: 14 стъпки (със снимки)
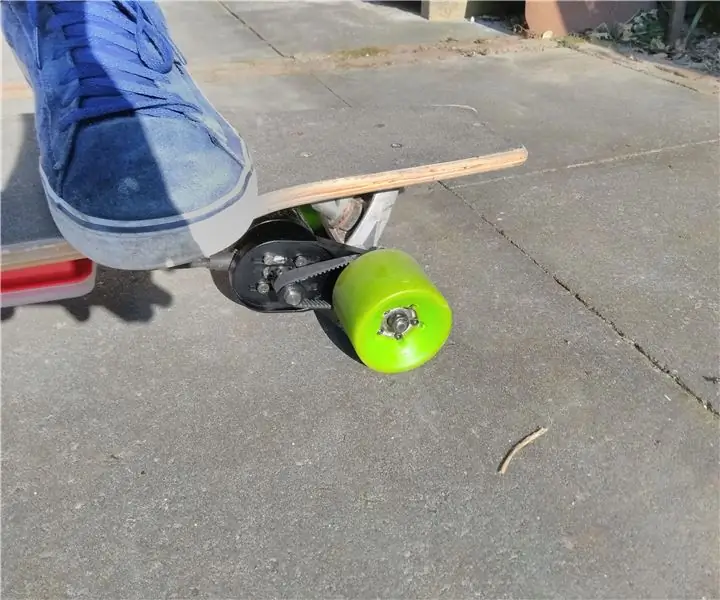
Diy Electric Skateboard: След 2 години проучване изградих първия си електрически скейтборд, тъй като видях инструкции как да изградите свой собствен електрически скейтборд, бях влюбен в diy електрически скейтборд. Изработването на собствен електрически скейтборд е форма на